If you've ever worked on a vintage Japanese motorcycle you've almost certainly struggled with countless buggered-up cross head screws. The usual recommendation to avoid further screw mangling is to put aside your old Phillips screwdrivers and get some "JIS" ones instead.
There is a lot of confusion about this topic and - to find out why some screwdrivers work on old Japanese equipment and others don't - we have to delve into the murky world of industrial standards.
- the international standards for crosshead screws and screwdrivers were harmonised decades ago and any decent quality modern screwdrivers made to current standards - as specified by JIS (Japan), DIN (Germany), BSI (UK), IS (India), ASME (USA), ISO (International) and so on - are made to the same tip dimensions and will work with the current ISO standard screws and the JIS fittings used on old Japanese motorcycles and cars.
- It is not true that the original JIS standard was updated to improve compatibility with US Phillips screws in a way that compromised the fit with Japanese screws. The Japanese standard has not changed since the 1950s, has always worked with both Phillips and Japanese screws, and is the basis for the international standard that was subsequently adopted globally.
- The dot mark that appears on the head of some JIS standard screws is a convention carried over from the initial harmonisation efforts that started in the 1960s (the dot was used to alert mechanics that the thread sizes on some screws made to the updated standard were no longer compatible with older equipment). Some Japanese fastener manufacturers still use the 'dot' today, although it is not mandatory.
- The harmonisation of standards for the small crosshead screws used in precision equipment like cameras has lagged behind and incompatibilities between screws and drivers may still occur.
- The idea that Phillips designed his crosshead screws and drivers to 'cam out' under torque is an urban myth with no evidence to back it up.
- Some screwdrivers are better than others - Vessel come highly recommended.
read on if you want to know the details.
National Industrial Standards
The first national standards body, the Engineering Standards Committee (now called BSI) was founded in the UK in 1901, and over the next couple of decades equivalent organisations were formed to manage the standards in other countries including ANSI in the USA, DIN in Germany and JISC in Japan[1]
Despite some early attempts to co-ordinate standardisation work internationally, national standards were generally created in isolation and this made it difficult for parts and tooling to be reused in different countries. These difficulties were brought into sharp focus during the second world war, which required allied countries to coordinate global industrialisation work on a massive scale, and shortly after the war ended the United Nations asked the International Federation of the National Standardizing Associations to form a new global standards body - the International Organization for Standardization (ISO) - to accelerate the adoption of common standards.
Unfortunately for all of us, one area where countries had diverged was on the standards for screws and other fasteners.
Japanese Industrial standards
The Japanese industrial standards (JIS) cover all aspects of Japan’s vast industrial endeavours and the responsible committee (JISC) maintains thousands of specifications.
This is the first source of confusion: strictly speaking, there is no such thing as "JIS screwdriver" or a "JIS screw", rather there are screws and screwdrivers that do (or do not) conform to the relevant Japanese Industrial standards for these items. Several standards apply, including:
- JIS B 4633 - Screwdrivers for cross recessed head screws
- JIS B 1012 - Cross recesses for screws
- JIS B 1111 - Cross recessed screws
The second cause of confusion is the frequently repeated claim that the "JIS Standard" became obsolete in the 2008. This is wrong, obviously, since the Japanese Industrial Standards extend to many specifications and Japan - like everyone other industrial economy - still needs a domestic standards body to maintain them.
The source of this misunderstanding seems to be a statement that at one time appeared on the website of the official US importer of Vessel screwdrivers:
Why Vessel's screwdrivers are not labeled “JIS”?
As you might know, Vessel is the oldest screwdriver manufacturer in Japan, and made a contribution to set a Japanese Industrial Standard (JIS) standard.
We do follow JIS (Japanese Industrial Standard) standard for cross point screwdrivers. Because the technology to manufacture screwdrivers in Japan had already become above a certain level, JIS (Japanese Industrial Standard) recognition system for screwdrivers became extinct in 2008.
So there is no authorized JIS (Japanese Industrial Standard) manufacturer now, and we therefore cannot print "JIS" mark on our screwdrivers.
Allowing for the dodgy translation, it seems that what is being explained here is that while Vessel continues to follow the JIS standards for crosspoint screwdrivers, they are no longer accredited to JIS manufacturing standards (they now comply with the globally recognised ISO 9001 standard instead), and this is why they no longer include JIS product certification mark on their products.
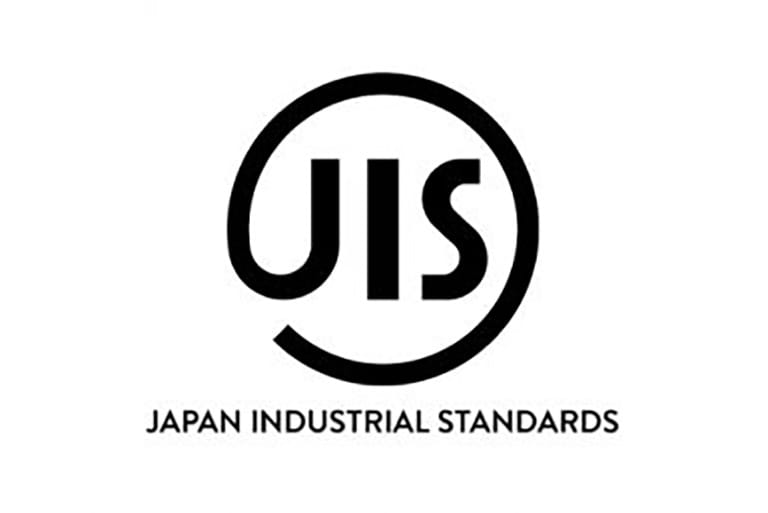
Note this is a reference to industrial quality standards and nothing to do with the dimensions of screws and screwdrivers.
It is also not true that the JIS standards for screwdrivers and screws are obsolete - the standards are still live - although, as we shall see, it is true that they are now largely harmonised with international standards.
This process started when JISC became a member of ISO in 1952.
The JIS screw "dot"
If you own any vintage Japanese vehicles you may already be familiar with one of Japan's early attempts to move closer to internationally recognised standards: in 1967 JICS decided to adopt aspects of the ISO standards on the thread dimensions of screws and bolts. This is how Honda, Japan's largest vehicle manufacturer at the time, announced the change:
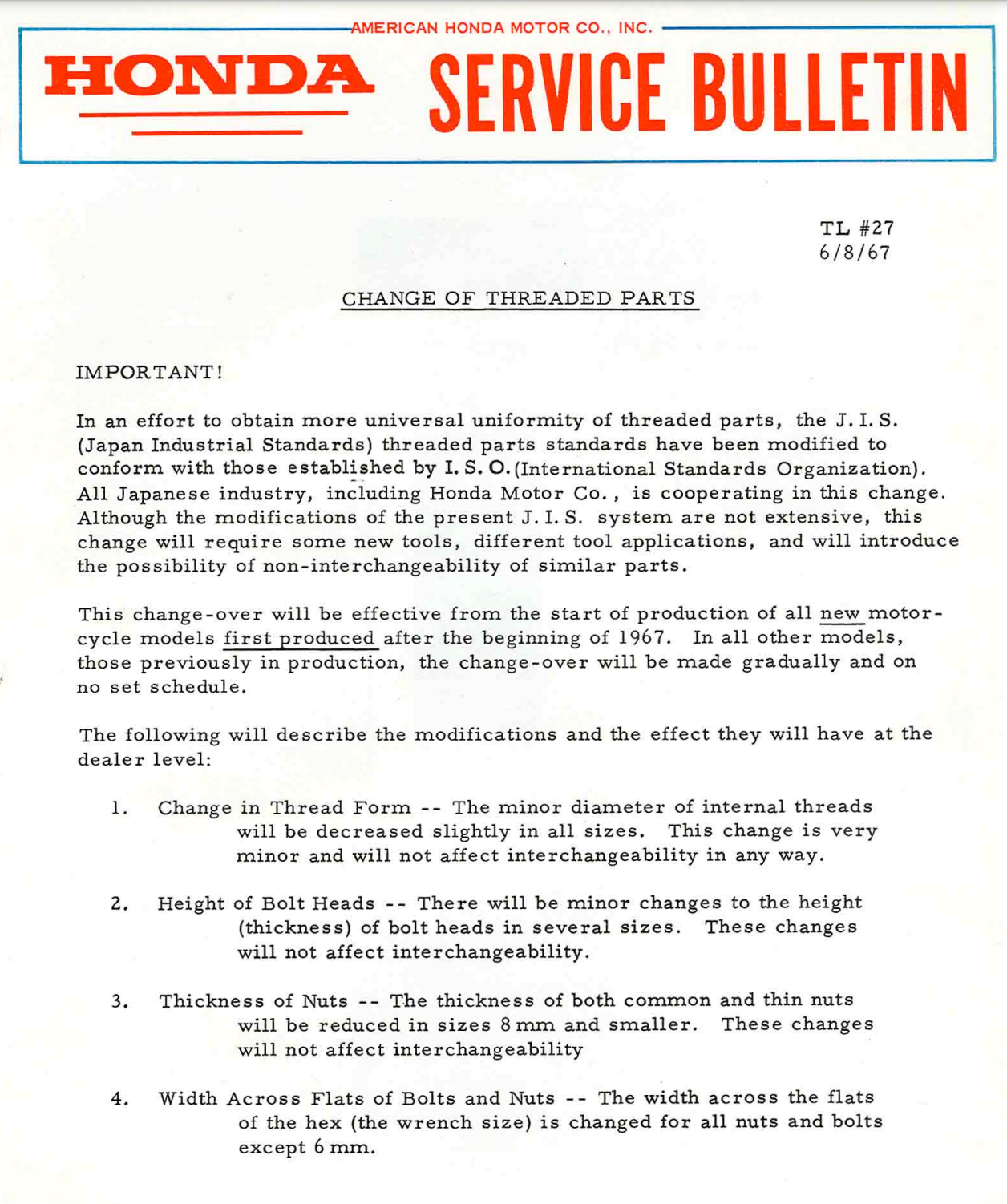
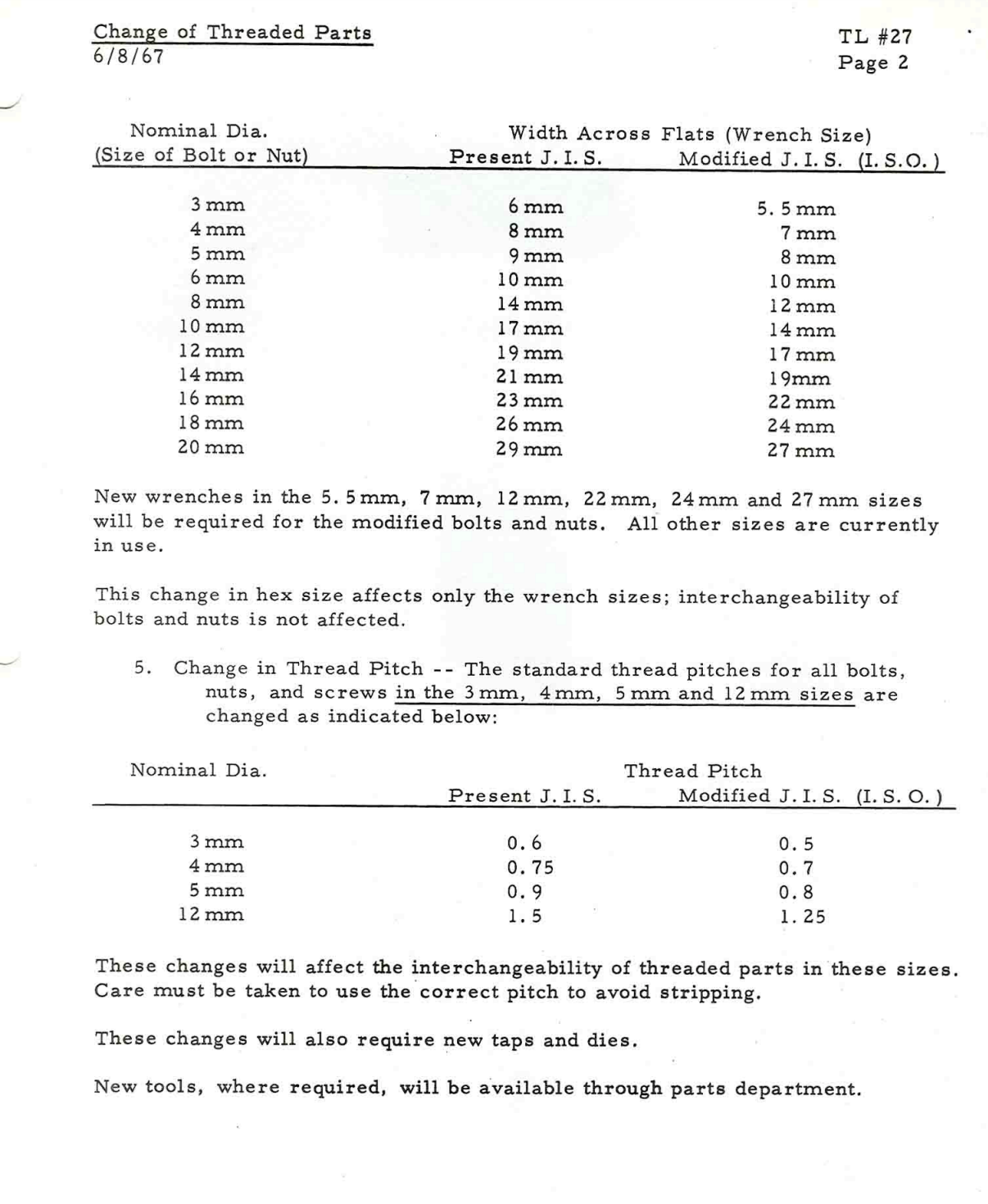
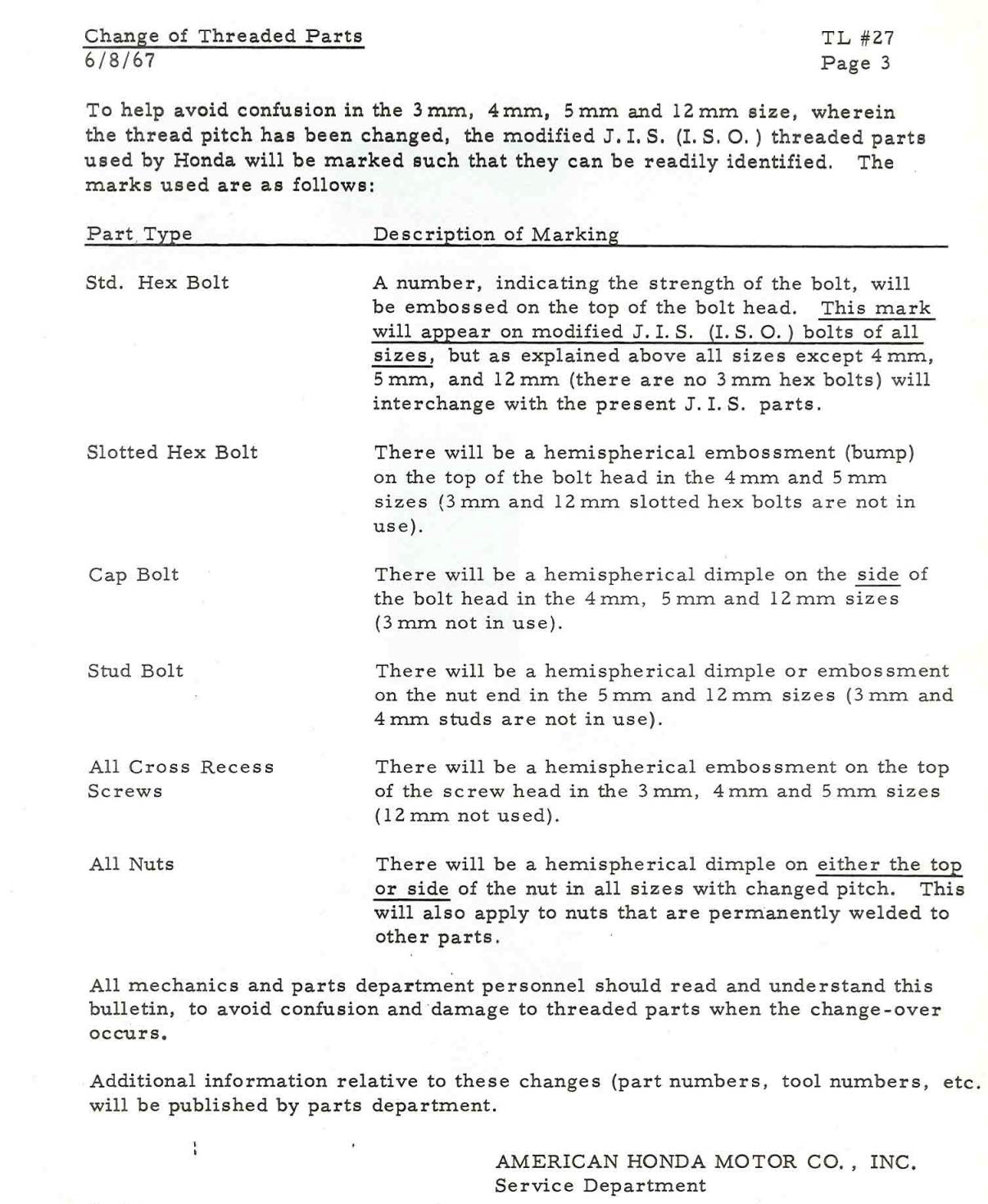
Honda Service Bulletin - August 1967
One of the changes made by the JISC was to update the rules for "width across the flats of Bolts or Nuts" and, although you might imagine this would be a straightforward standard to agree on, it got caught up in the ongoing wrangling over which fastener standards should form the long term basis for the international rules. Until the late 1970s, the US were trying to get a new scheme - the "Optimum Metric Fastener System" - agreed that matched neither the German DIN nor the JIS currently in use.
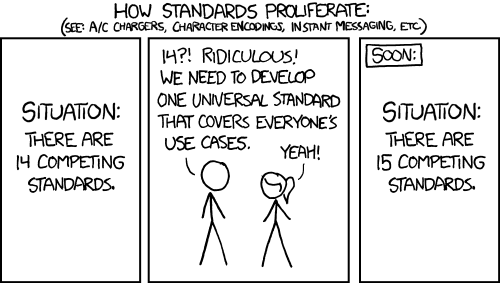
The "Optimum" standard was subsequently abandoned, and everyone signed up to the original ISO proposal instead, but the 'width across the flats' standard never got properly sorted out and if you need to undo a 10mm bolt on vintage vehicles made in Germany, Japan and the US you will probably need three different spanners.
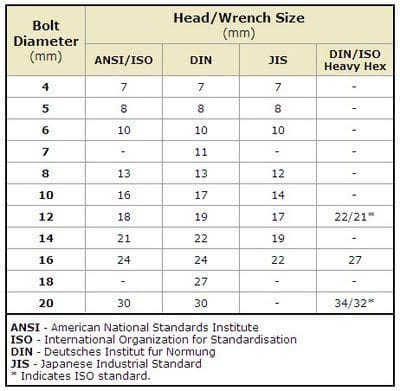
The more significant change made by JISC in the 1960s related to thread pitch. To conform with the ISO specifications it was necessary for the 3, 4, 5 and 12mm screws and bolts used in Japanese manufacturing to adopt a new thread pitch. Because the screws made according to the new standard would no longer fit older products, it was decided that a "hemispherical dimple" would be placed on the heads of the altered screws to alert mechanics of the change. In practice Honda's suppliers went on to mark the screws with either a + (plus) symbol or a ° (dot) and they used the mark on all screw sizes, including those where there had been no change to the thread pitch.
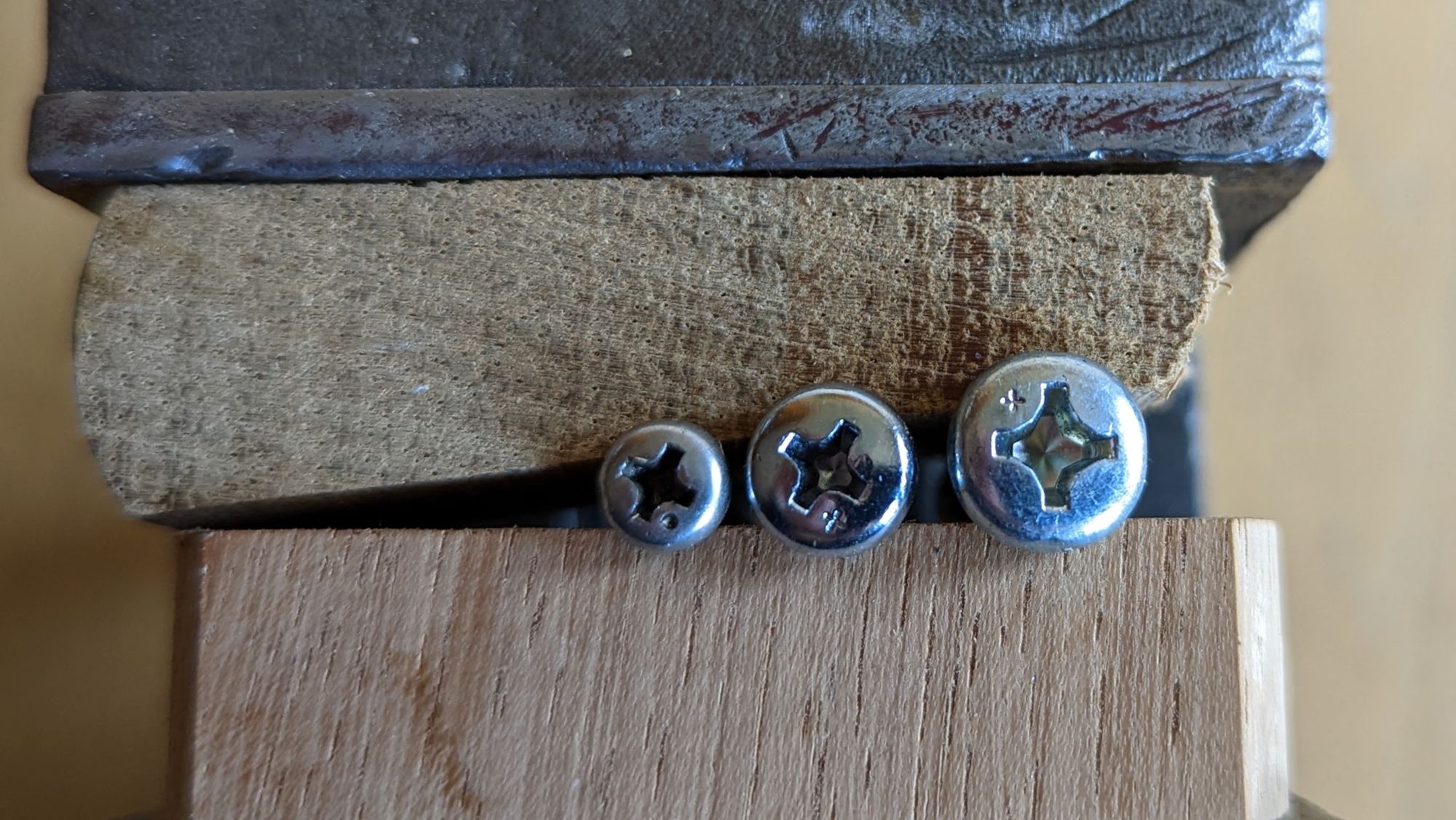
These marks are still used on some modern Japanese screw heads, but it is not required.
JIS and ISO crosshead screws.
Conventional wisdom has it that standard Phillips cross head screwdrivers are not a good fit for screw heads made to the JIS standards, and this suggests that there is something about the JIS cross-head standards that differs from specs used in other countries. And indeed, there are separate JIS and ISO standards for the Cross Recesses for Screws:
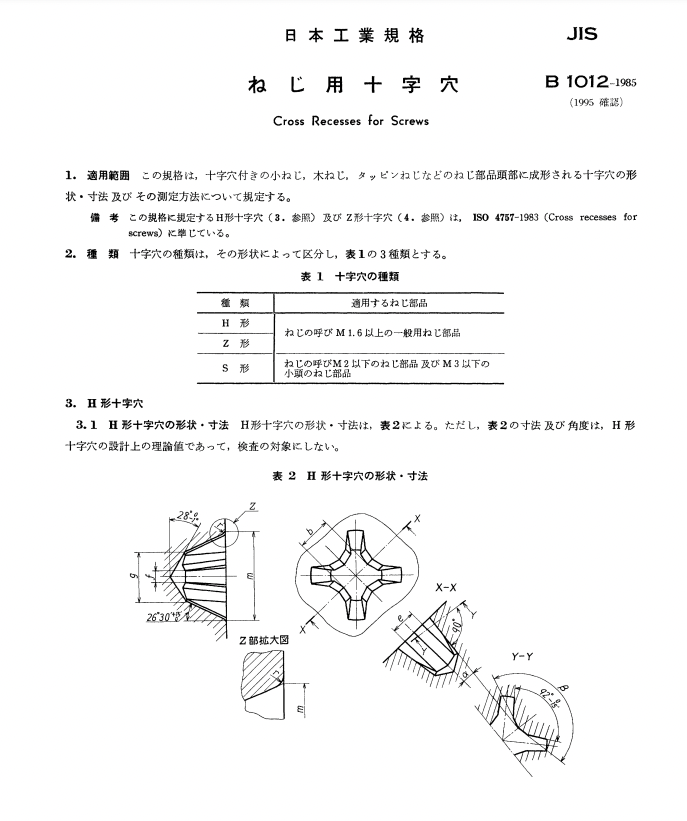
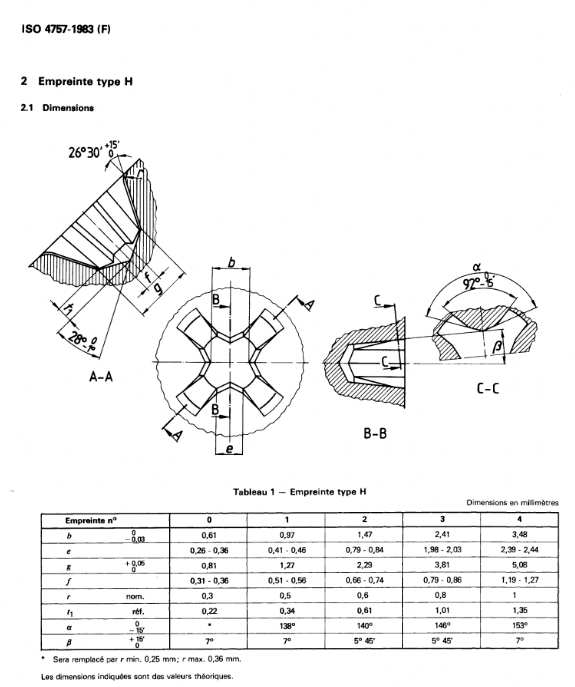
The Cross Recesses for Screws standards: JIS (left) and ISO (right)
However, the forward to the 1995 JIS standard says:
the H-shaped cross recesses (phillips) and type Z cross recesses (pozidriv) specified in this standard conform to ISO 4757-1983 (Cross recesses screws)[3].
Unsurprisingly, a similar story applies to the standards for the screwdrivers that are used with these screws...
JIS crosshead screw drivers
JISC had their own screwdriver specification (JIS B 4533) which was introduced in the 1950s. The current standard is aligned with the ISO equivalent standard, as explained in the prefix of the 1998 version of the standard:
This standard is based on the international standards shown in the remarks. The main body defines the types and grades, shapes and dimensions, quality, inspection, product designation and labelling that were previously defined in the Japanese Industrial Standards.
The following international standards correspond to this standard:
ISO/DIS 8764-11996 Assembly tools for screws and nuts Screwdrivers for cross recessed head screws-Part 1: Driver points
ISO 8764-2: 1992 Screwdrivers for cross-recessed head screws - Part 2: General requirements, lengths of blades and marking of hand-operated screwdrivers
This standard stipulates Phillips screwdrivers used for threaded parts with H-type and S-type cross recesses of JIS B 1012.
Given that the work to adopt common standards happened over 20 years ago, you may well be wondering what the fuss about "JIS" screws and screwdrivers is all about. The answer lies in the US of A.
Fasteners in the United States
It is sometimes, rather unkindly, said that America is one of the three countries left in the world (the others being Burma and Liberia) determined to cling on to the imperial measurement system. In practice, the vast majority of manufacturing and science done in the US nowadays is based on international metric standards and it would be fairer to say they are in the unhappy group of countries - including the UK - where the metric and imperial systems continue in an uneasy coexistence.
The United States first started to make significant moves to metric fasteners in the 1970s when Ford, Chrysler and GM agreed to use the metric system. Given the importance of these businesses the major suppliers of fasteners soon followed suit. This commitment to metric by the US auto industry was a big deal as it paved the way for cars designed for the US market to be sold all over the world, and for parts produced in one country to be incorporated into machines made in another with no change to tooling. Given the huge economic opportunities this enabled, it was inevitable that other US manufacturers would be hot on the heels of the big three auto manufacturers, and this is what happened.
However, before we got to this point the US had their own version of crosshead screws, named Phillips after the man who patented the design. Although today the term "Phillips" is used generically to describe crosshead screws, when it was first introduced it was a unique design that had to be licensed by any manufacturer wishing to use it.
Phillips crosshead
As you will see from the 1936 patent (below), these screws were designed to be self centring and, when wedged in place on the tip of the screwdriver, allowed screws to be installed with one hand, a big advantage over the slot head screws used at the time that helped speed up work on fast moving assembly lines.
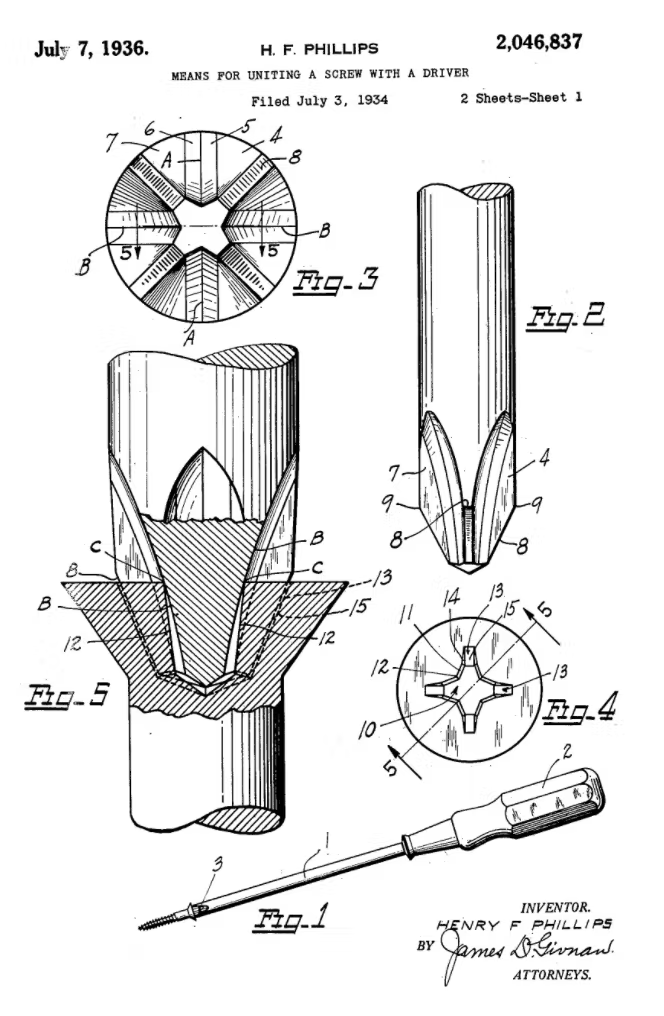
The design was adopted by Ford and quickly established itself as de facto stadard
Cam out
An urban myth has evolved that Phillips screws were designed to 'cam out' when too much torque is applied. It is not clear why Phillips would have intentionally created a design that would cause the screwdriver to pop out of the screw head in an uncontrolled manner - risking damaging the screws or their surroundings - or why, if he believed this was a genuine benefit, it was not mentioned in the patent[4].
The more plausible explanation is that it is simply a deficiency in the originally design (a defect that numerous inventors went on to try and improve upon, most notably GKN Screws and Fasteners, who patented the pozidriv design).
The myth does have legs though, and here is an example of Black and Decker availing themselves of some poetic license about the older Phillips screws to justify their own invention in a patent application from 1971:
the Phillips screw was designed to center quickly and easily on the screwdriver and permit more torque to be applied to the screw so that it would hold tighter than conventional slotted screws. In addition, it was expressly contemplated that, when applied by automated screwdrivers on an assembly line, the increasing torque applied to the Phillips screw would eventually cause the driver to pop out of the recess in the screw. In other words, the original Phillips-head design was intended to cause cam-out of the driver without damaging the screw head, it is, of course, this tendency of the Phillips head design to cause cam-out of the driver, that is a principal source of irritation for craftsmen and ordinary consumers alike.
... an assessment of the original design that is not backed up by evidence.
Having said all that, it still true that the design does have an unfortunate tendency to cam-out, and the problems seems to be particularly apparent when using older US screwdrivers on Japanese screws (some US mechanics working in the 60s and 70s resorted to filing the ends of their screwdrivers in an attempt to get a better fit on Japanese screws).
Standards Harmonisation
The ISO crosshead screwdriver standards - and thus all the national standards that align to it (including US, Germany, Australia, UK etc) - are based on the original Japanese standard. This is illustrated below by the screenshots from the 1954 B4633 JIS standard, the US (ACME) B107.30 standard and the ISO 8764-1 standard
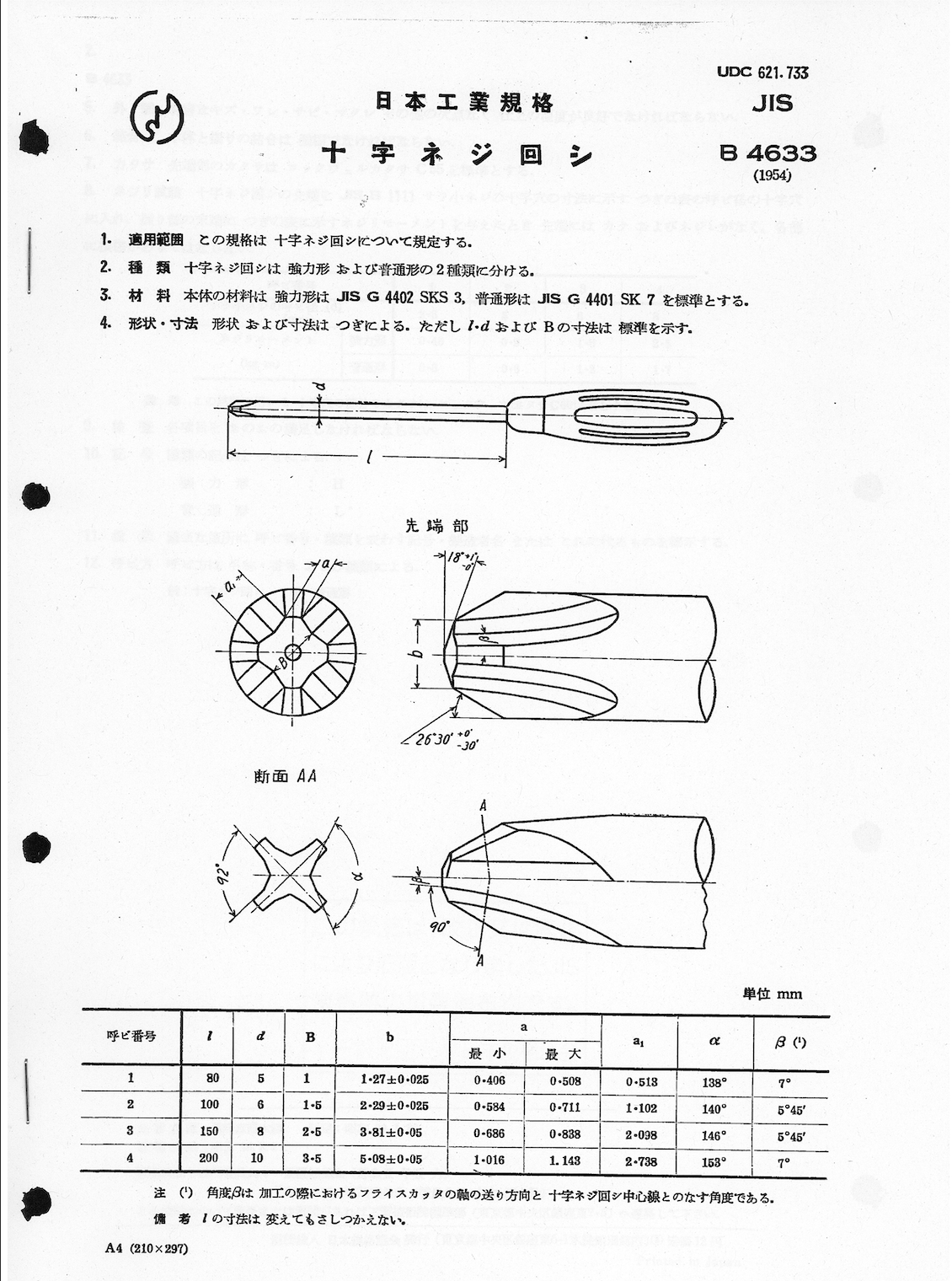
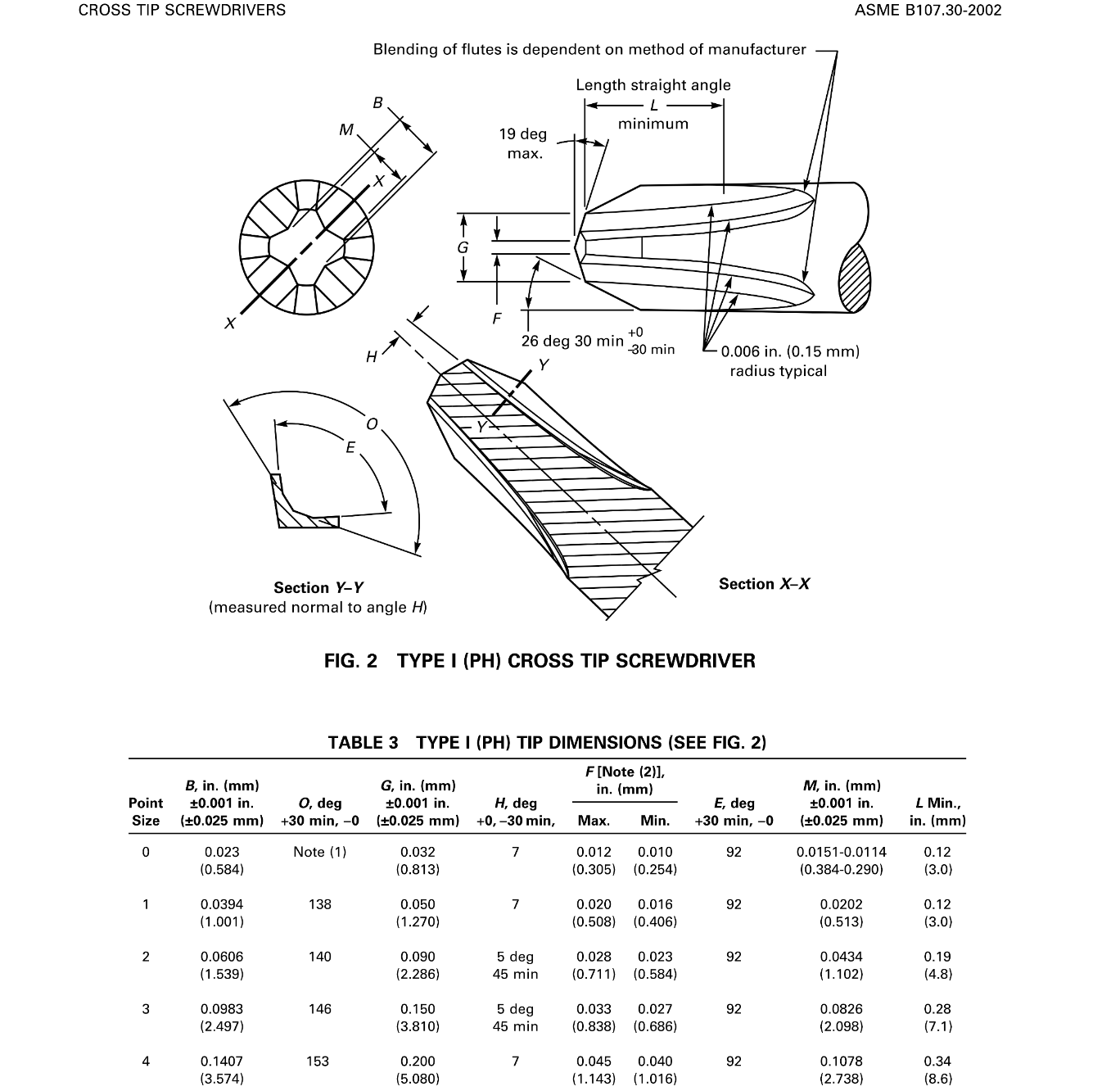
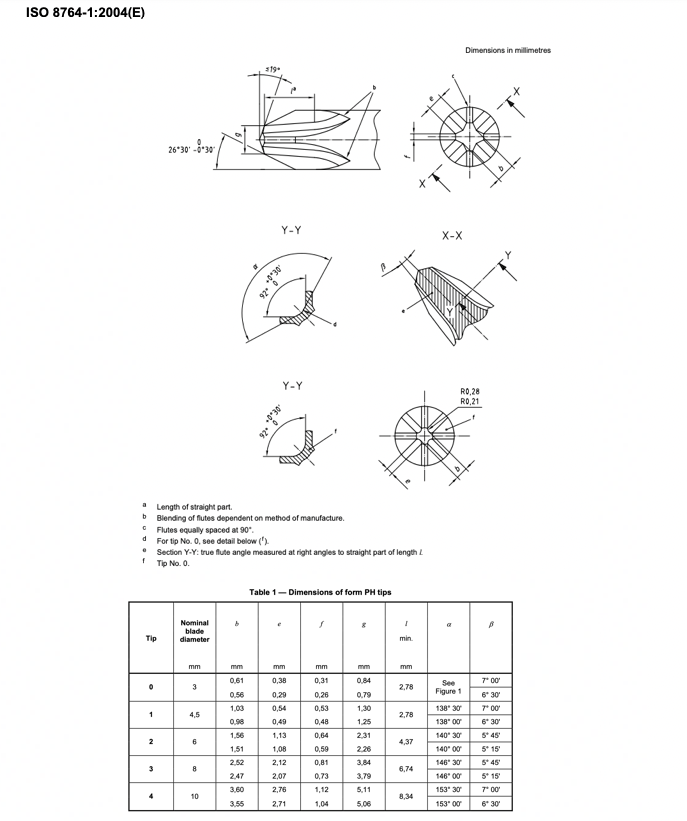
Many thanks to Brandon V at the Garage Journal Forum who tracked down these standards
I've transcribed the dimensions below to make it easier to read. As you can see, the international standards are aligned with the original JIS specification, bar the addition of a couple of manufacturing tolerances not referenced in the old standard.
JIS B4633-1954
Tip angles: 18° (+1° -0) / 26°30' (+0 -30') / 92°
ASME B107.30-2002
Tip angles: 19° max / 26°30' (+0 -30') / 92° (+30' -0)
ISO 8764-1:2004
Tip angles: ≤ 19°/ 26°30' (+0 -30') / 92° (+30' -0)
The UK (BSI) and Germany (DIN) standards organisation had also aligned their crosshead screwdriver standards with the ISO version before the end of the last century.
So there you have it, any screwdriver tip manufactured to the current international standard will also conform to the original JIS specification from the 1950s and should be good for crosshead screws wherever they were made in Japan, Europe or the USA.
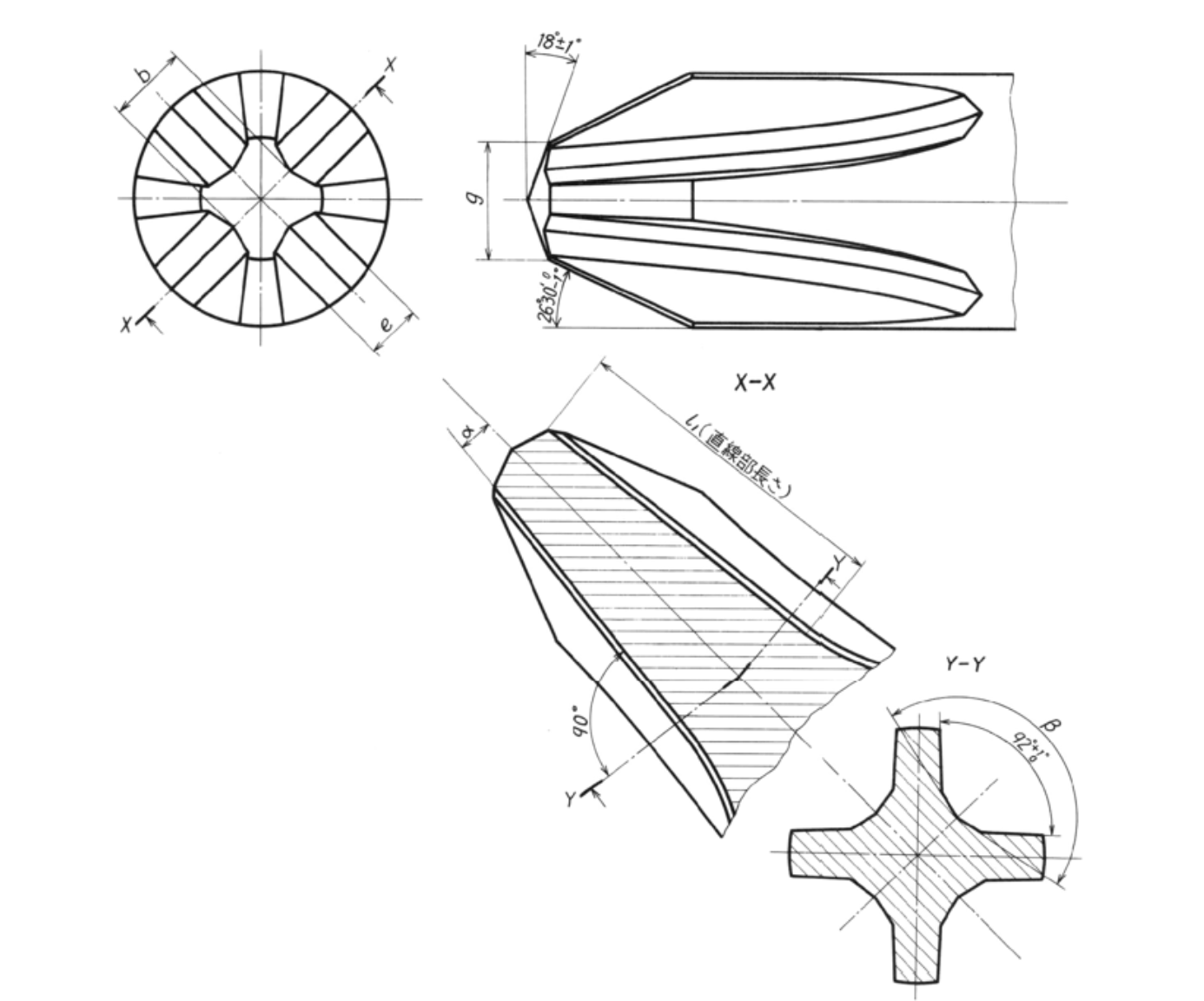
Screw head diameters
One area where the standards related to crosshead screws has not been harmonised between JIS and ISO is the head size, and Japanese screw heads are smaller than the ISO equivalent
For instance, the diameter of the head of a JIS standard M6 screw is 10mm whereas the ISO equivalent is 12mm; a M5 is ~8mm vs 9.5mm for ISO and so on.
This makes no difference functionally of course, although the smaller heads can be handy where there is limited space and the bigger ISO heads are not 'right' when used on vintage Japanese bikes where you are trying to keep things as close to the original as possible.
Vessel
Vessel, the oldest screwdriver maker in Japan, were founded in 1916, twenty years before the Henry Phillips patented the Phillips cross head screw design.
Vessel had originally licensed the Phillips patent and, once it expired in the late 1950s, were one of the businesses to help design a replacement national Japanese standard for crosshead screws and screwdrivers. It seems that the new JIS standards departed somewhat from the original patent design and, although presumably backwardly compatible with the original Phillips screws that had been in use in Japan up to that point, created problems with the older Phillips screw drivers (some US mechanics recall filling the end of their US made screwdrivers to get them to fit the screw heads on Japanese bikes of the 60s and 70s).
Since then - as explained above - the Japanese standards have been harmonised with the ISO standard, which as explained by Vessel is "Compatible with ISO, JIS and Phillips Standard Screws."
Electronic equipment screws
The small screws used in precision instruments are yet another source of confusion, since although the harmonisation work on the larger crosshead screws has made good progress, the work to harmonize screws used in Japanese cameras and the like has lagged behind. This slide from Vessel Europe highlights some difference between the JIS/ISO No. 0 crosshead driver and the version promoted by the Japan Camera Industrial Standard (the de facto standard until recently)
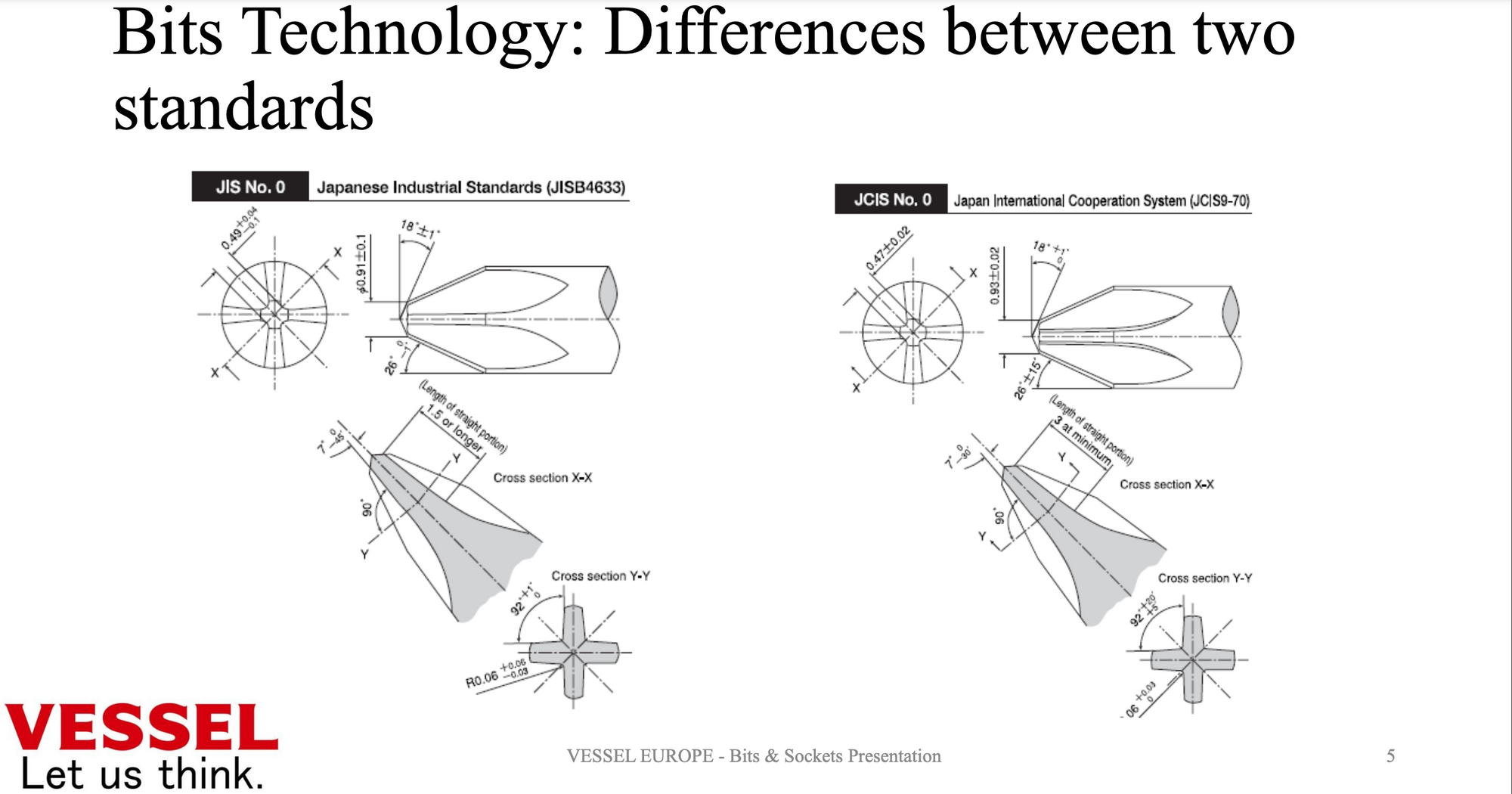
Testing
I did a number of tests on Japanese (Honda) 5mm machine screws using a motley crew of #2 crosshead screwdrivers

I won't bore you with the details of tests as the results were inconclusive. My main observations were:
- There was no discernible difference in fit between the Vessel, Wera and Kennedy screwdrivers
- The Stanley popped out of the screw more easily than the rest
Although the Stanley was noticeably poor, I do not know if this is because it was made to a different (American) specification or just because it is more cheaply made than the rest. Similarly, although I prefer using the Vessels, they are also the most expensive out of the test set.
I did a bit more testing with my #3 screwdrivers using some Japanese 6mm screws of various vintages:
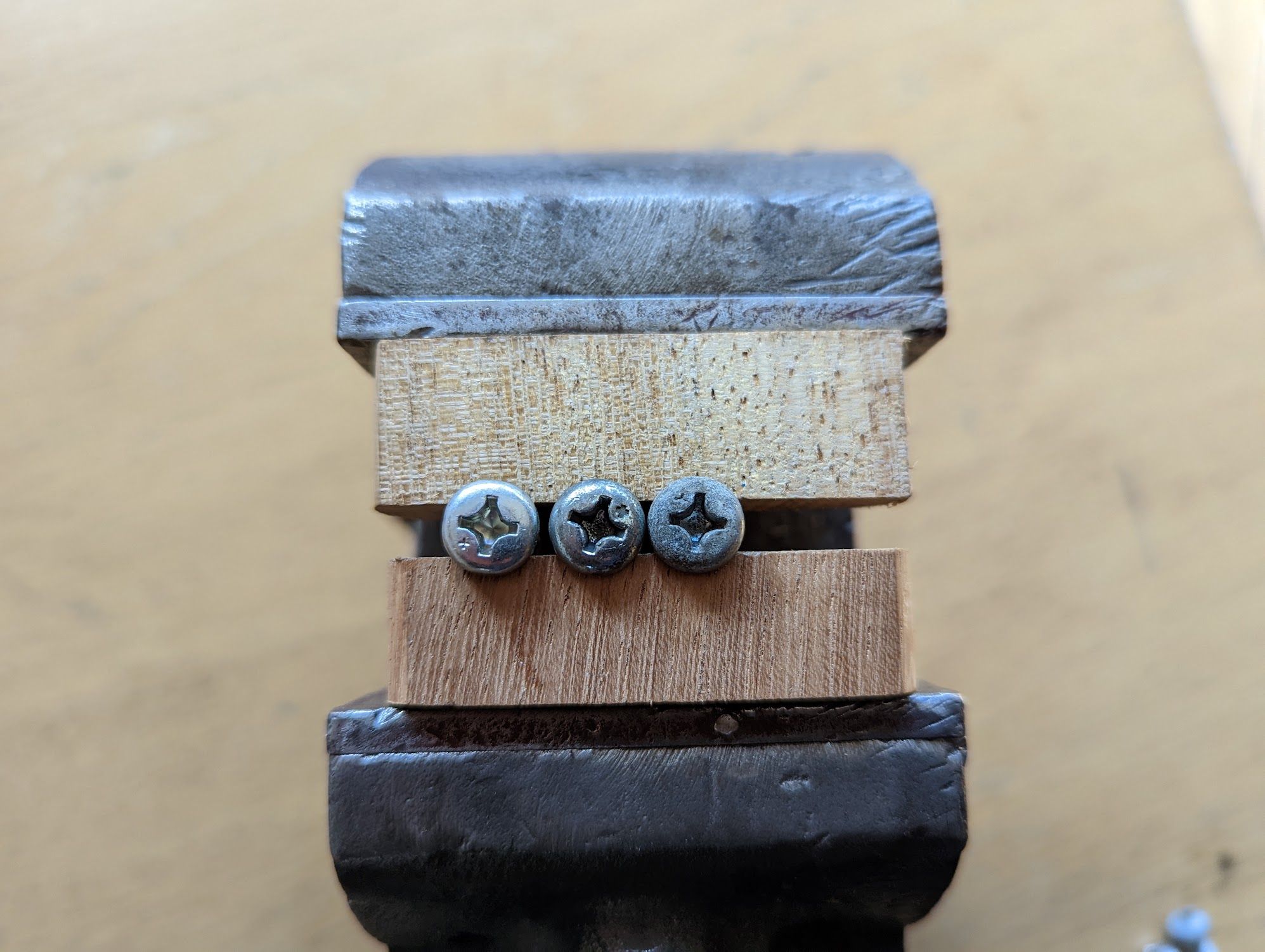
The #3 drivers from Wera, Kennedy and Vessel seemed to fit identically in all the screw heads. I did note the Vessel Megadora model had a slightly vague feel when locating it in the screw head but I think this is a consequence of the serrated "jawfit" edges this model uses. Jawfit really does work by the way: it exerts sufficient "grip" so that I could twist the screwdriver in the screw head and lift he heavy engineers vice shown above. A video demonstration of the same is below:
I also fished out the screwdrivers from the Kowa toolkits that came with my old Hondas, one from the 70s and one from the 60s. There was a clear visual difference between the two, with the older versions being noticeably narrower at the tip:
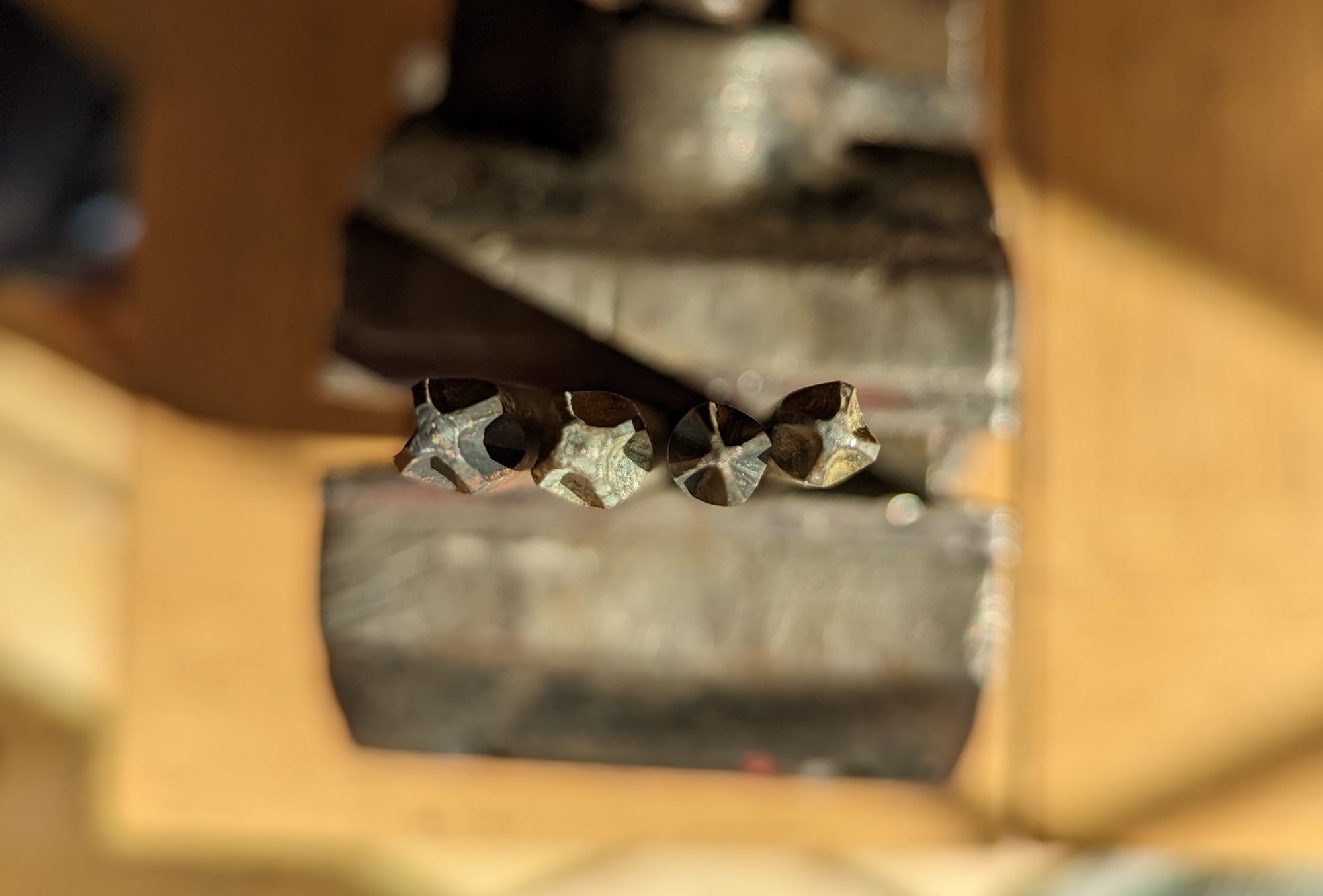
Sadly the performance of one set over the other did not correspond to the relative age of each of the test screws (the older/narrower drivers performed worse on all three screws). As a result I don't really know if the difference in tip shape is an indicator of changing screw/screwdriver designs over time or just due to a combination of manufacturing differences over the years and the shonky state of my 40+ year old screws.
Conclusion
Screwdrivers made to conform to modern ISO standards are designed to work with the crosshead screws fitted on old Japanese motor vehicles and are also compatible the original Phillips screw designs. Of course the existence of common standards does not necessarily mean all manufacturers have adopted them, but you'd like to think that things are heading in the right direction.
This video shows a Vessel screwdriver performing better than a random US Phillips driver.
If you do find yourself struggling with your current screwdrivers when working on Japanese vehicles - and you probably will, given the likelihood that screws have been mangled during previous work performed on these older machines - then you might like to consider the screwdrivers made by the Vessel. After all, if the oldest screwdriver maker in Japan doesn't know how to make a driver that works well with Japanese screws then who else will?
A tragicomic footnote: this whole cross-head screw nonsense might have been avoided entirely if only we'd all adopted the Roberson square drive.
References
1 | the original committee formed in 1917 was called the Japanese Engineering Standards Committee and it was renamed to the Japanese Industrial Standards Committee (JISC) in 1949. ⏎ |
2 | this is the latest sizing for JIS nuts and the result of further standardization shenanigans that meant the 14mm M8 nuts used on the engine studs of the 6vs from the 60s and 70s are now only supplied by Honda in the new 12mm form. ⏎ |
3 | The JIS standards refer to three different recesses types H= standard cross head; Z = pozidriv cross head (not to be confused with the standard cross head!) and S for small camera screws. The standard crosshead and pozidriv tip profiles are generally abbreviated as PH and PZ respectively although some Japanese manufactuers, including Vessel, refer to their standard crosshead drivers as "P" tips. ⏎ |
4 | ... indeed the continuation patent,US2046839, filed in the same year specifically says "One of the principal objects of the invention is the provision of a recess in the head of a screw which is particularly adapted for firm engagement with a correspondingly shaped driving tool or screw driver, and in such a way that there will be no tendency of the driver to cam out of the reces when united in operative engagement with each other. ⏎" |
5 | the Kennedy is the only one the manufactures advertise as conforming to a standard (ISO 8764-1). ⏎ |